“Hey Jim, isn’t it cool that this machine can disinfect our office? I can’t wait to try it!”—The evolution of technology continues to impress us with new features and application for disinfection. With the trending news of COVID-19 infection cases increasing around the world, fogging and automated disinfection machines are becoming more in demand in the medical, public ,and industrial areas. But many have wondered, how would one know if the machine is doing a good job at eradicating harmful pathogens around its surrounding surfaces? International regulators have implemented a new requirement for all automated disinfectant machines to be in compliance with the European Standard EN 17272. Published in 2020, this standard not only evaluates the efficacy of the disinfectant dispensed by the machine, but also the distribution capabilities of said machine. Revolving around a broad spectrum of antimicrobial activity, this European standard might as well be the new face of Microbiology Vogue.
What is EN 17272:2020?
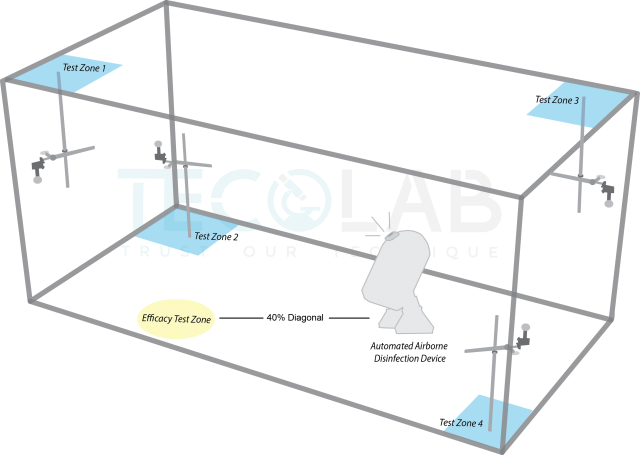
“Wait! Does this mean we can use this machine to disinfect viruses in the air?”—EN 17272 was developed by the European Committee as a guidance to evaluate the disinfection activity of an airborne disinfection system towards various groups of harmful microorganisms in the medical, veterinary, food, industrial, domestic, and institutional areas. The term ‘airborne’ describes the manner by which the disinfectant is dispersed—either by gaseous, vapor, and/or aerosolized form. It does not disinfect the air but the surfaces present in an enclosed area of system application. The airborne disinfection system is inclusive of an automated dispersing device and its complementary disinfectant solution. These are to be assessed according to two mandatory parts conducted separately: Part 1 Efficacy Test and Part 2 Distribution Test. Part 1 is conducted to evaluate the minimum efficacy requirement of each antimicrobial activity to be claimed in the respective application areas whereas Part 2 evaluates the efficacy of distribution process throughout an enclosed area.
Which Phase Should You Conduct First?
“Am I suppose to conduct Part 1 or Part 2 first?”—We would advise manufacturers to start with the distribution test. This is done by inoculating only Staphylococcus aureus on sterile stainless steel discs and place them in all four test zones as shown in the illustration above. Once the disinfection cycle is over, the remaining viable bacteria is recovered. A 5-log10 reduction would deem a machine capable of distributing its complementary disinfectant solution effectively. This is because, evaluating the distribution efficacy of the automated device gives us an insight on how well your machine distributes the disinfectant to its surrounding.
What are the Antimicrobial Activities that Can be Claimed?
“Why would you call it the new face of Microbiology Vogue?”—Part 1 Efficacy Test envelopes a rather broad spectrum of antimicrobial activity. This norm specifies the preparation and biocidal activity requirements towards bacteria, yeasts, fungi, enveloped and non-enveloped viruses, mycobacteria, bacterial spores, and bacteriophages. Thus, it’s an all-in-one test favored by all disinfection system manufacturers. The table below summarizes the test organisms and passing criteria for each antimicrobial claim. “R” represents the passing log reduction criteria of each group of organism in each application areas.
APPLICATION AREA | BACTERIA | R | FUNGI & YEAST | R | VIRUS | R | MYCOBACTERIA | R | BACTERIAL SPORE | R |
Medical Area | Staphylococcus aureus Enterococcus hirae Escherichia coli Acinetobacter baumannii |
5 | Candida albicans Aspergillus brasiliensis |
4 | Murine norovirus Human adenovirus |
4 | Mycobacterium avium Mycobacterium terrae |
4 | Bacillus subtilis | 4 |
Veterinary Area | Pseudomonas aeruginosa Staphylococcus aureus Enterococcus hirae Proteus hauseri |
5 | Candida albicans Aspergillus brasiliensis |
4 | Porcine parvovirus | 4 | Mycobacterium avium | 4 | Bacillus subtilis | 3 |
Food, Industrial, Domestic & Institutional Areas | Pseudomonas aeruginosa Staphylococcus aureus Enterococcus hirae Escherichia coli |
5 | Candida albicans Aspergillus brasiliensis |
4 | Murine norovirus Human adenovirus Lactobacillus lactis P001 Lactobacillus lactis P008 |
4 | Mycobacterium avium Mycobacterium terrae |
4 | Bacillus subtilis | 3 |
During Part 1, the microorganism of interest is inoculated on sterile metal discs and placed at a 40% diagonal distance from the automated device in the enclosed room. The test zone for efficacy test is shown in the illustration above. The automated device is then activated and let run for the duration of its cycle that is pre-determined by the size of the enclosed area. Once the cycle is over, the surviving microorganisms present on the steel discs are recovered and plated. The log reduction is then determined. The minimum antimicrobial spectrum activity required to be assessed are bactericidal activity and yeasticidal activity.
What are the Factors Affecting Your EN 17272 Test Result?
There are a few factors that can affect your test results during EN 17272. One being, choosing the right active substance. When choosing for the right active ingredient in your disinfectant, there are a few criteria to consider when making the final decision. These criteria includes the antimicrobial efficacy spectrum of the active ingredient, material compatibility of disinfectant towards the automated device and its surrounding surfaces, and the duration of kill effect.
Active substances used in air disinfection processes are usually those that produce a reactive active substance that kills a target organism such as Hydrogen peroxide. Hydrogen peroxide produces hydroxyl free radicals that cause microorganism cell destruction. At an optimal concentration, this active substance is also environmental friendly as it degrades to water and oxygen when exposed to the environment and does not leave residue.
Apart from active substances, the airborne disinfection contact (ADC) time also plays a crucial role in achieving good results. ADC time is normally pre-determined according to the size of an enclosed area. It starts from the first dispersion of the disinfectant into the surrounding, up to the start of aeration time. The duration of ADC time allows an adequate amount of disinfectant to be dispersed by a suitable pressure from the machine, exposing the entire room with disinfectant. An optimum ADC time would allow full coverage of inanimate objects with the disinfectant.
The last stage of the airborne disinfection cycle would be the aeration time. Aeration time is the duration of which the disinfectant is left to react and/or degrade in the enclosed area before reaching a safe surrounding concentration for human exposure, in this case, to recover the inoculated stainless steel discs. Personal protective equipment (PPE) are encouraged to be worn in scenarios where the stainless steel discs are to be recovered during aeration time for research purposes. With an optimum aeration time, the disinfectant is given an adequate amount of time to react completely with the target organisms and ensures the safety of those entering the application room.
Do you have an automated airborne disinfection system ready for testing? Let us assist you with achieving your target product claims today!